The Indispensible Tool
Do you erect towers for utilities or conveyor systems for mines? Do you supply fabricated steel for bridges, ships or machinery? If you fabricate structural steel, PythonX STRUCTURAL will make your operation more efficient. That’s what it’s doing for a variety of companies who operate outside the traditional building industry.
Click on any name to learn how >>
So, whether you call it a beam, a brace or a bracket . . . whether you make it from carbon steel, stainless or aluminum . . . PythonX STRUCTURAL will help you make it at the lowest total cost and with unrivaled quality.
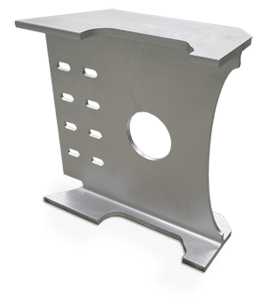
SSB STARK STAHLBAU GmbH – Startseite, Coburg, Germany
CHICAGO BRIDGE & IRON – Bangkok, Thailand
HIDAYATH GROUP – Dubai, UAE
THE MİTAŞ GROUP – Turkey
MANUFACTURAS METALICAS AJAX, S.A. de C.V. – Mexico
AJAX is one of Mexico’s largest structural steel design and fabrication companies, responsible for the skeleton of many of the most impressive modern buildings that grace the country’s large cities. visit web site >>